Plants
Used lube oils re-refining
Re-refining plants recover the base oil fraction from waste lubricant oils (lube oils).
The regenerated base oil, the main output of the process, is used as starting material for the production of lubricant oils, used for automotive, marine and industrial applications.
The remaining output streams are gas oil and bitumen, which are used as fuels (light fractions) and as additives for asphalt roofing manufacturing and paving.
Overview
Show more Show lessOur plants usually include the following refining steps and unit operations:
- De-watering/dehydration: the key unit operations are flash separation and vacuum distillation.
- De-fuelling (diesel oil separation) by evaporation: the key unit operation is a vacuum distillation column with or without a thin film evaporator used as a reboiler.
- Reaction: this unit is especially recommended when a high olefin fraction is present and its removal is required to meet the recovered base oil grade specification.
- Fractionation by distillation: the key unit operations require a vacuum distillation column with a thin film evaporator used as a reboiler.
Depending on the waste lube oil characteristics and on the desired base oil specifications, the process and the re-refining plant configuration may change compared to the one described above.
Features and rangeability
Show more Show lessWe customise the design of used lube oil re-refining plants according to the feed composition and the final product properties. Typical operating capacities are shown below:
- Feed flow rate: 1 t/h to 4 t/h
- Pressure: 1 mbar(a) down to 0,001 mbar(a) for special applications
Using a thin film evaporator as the main process unit facilitates handing the extremely viscous fractions normally present at the evaporator liquid discharge, thus achieving maximum solvent recovery.
Heat recovery from the heat exchanger network can be achieved to minimise energy consumption.
Re-refining plants can be supplied unassembled or preassembled on a modular skid, to minimise installation operations at the customer‘s site.
Construction materials are selected according to the possible contaminants present in the used lube oil feed (sulphur, nitrogen compounds) and the unit operations included in the treatment.
The main materials usually selected are the following:
- Carbon steel
- Stainless steel
- Duplex or super duplex stainless steel
- High nickel alloys
A wide range of services from technical feasibility studies to revamping existing plants is also available.
Key benefits
Show more Show less- Recovery of high-quality base oil without product degradation (e.g., cracking) thanks to:
- Low evaporation temperature achieved by vacuum operation
- Low residence time and high turbulence achieved by the evaporator high rotor speed and the thin density of the oil film on the evaporator wall
- Implementation of waste hierarchy
- Customised design
- Optimised thermal configuration
- Maximum energy savings
- High automation level
- Remote assistance and remote supervision services
Applications
Show more Show lessRe-refining can be used for different used lube oils, both mineral and synthetic, non-halogenated (chlorinated) or containing PCB compounds.
It is suitable for lube oils originating from different uses (engines, gears, turbines, compressors, machines) that can be classified into two main categories:
- Automotive waste oils (black oils)
- Industrial waste oils (clear oils)
We can support all companies active in used lube oil collection and re-refining services, by either:
- Modifying existing plants to improve capacity and/or performance (brownfield)
- Designing new regeneration plants (greenfield)
Given the great variety of industrial processes and solvent mixtures, we identify the specific solution to address customers’ needs by conducting tests at the laboratory and pilot plant scale, as well feasibility studies at our R&D centre.
References
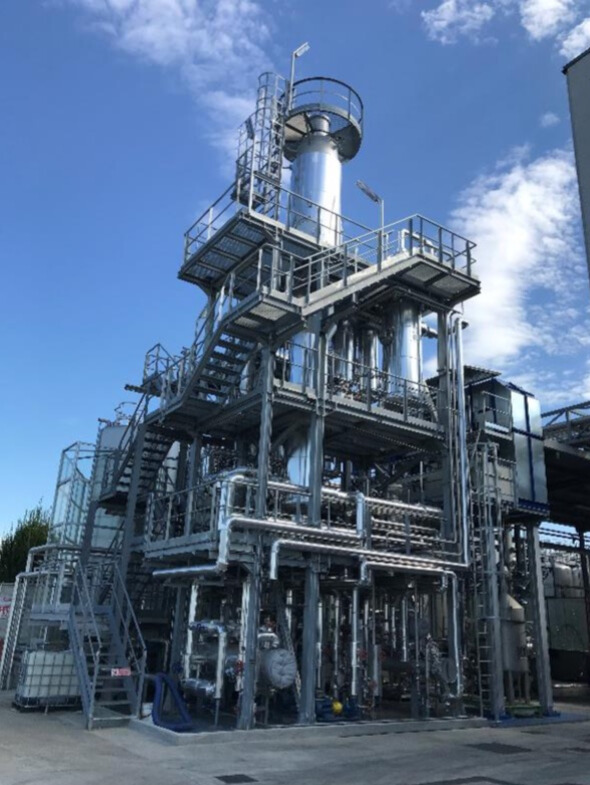
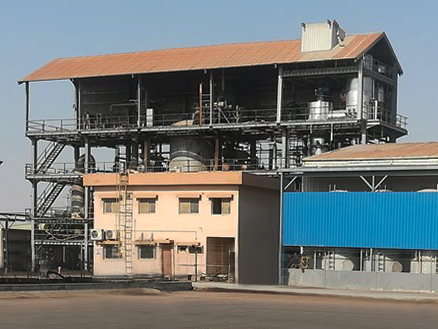
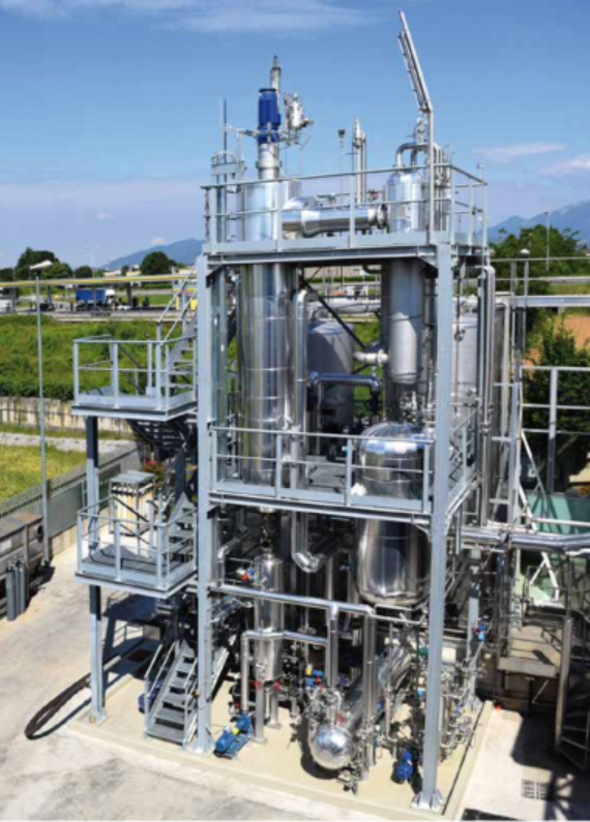
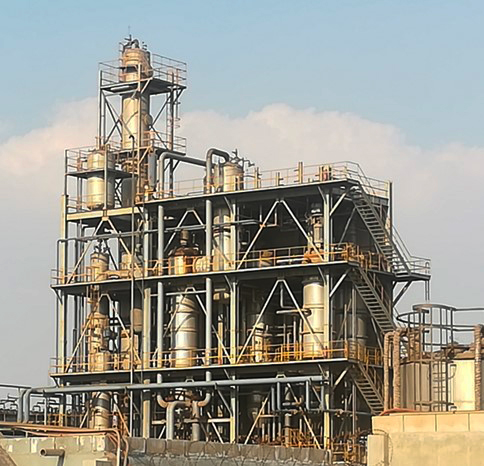