Plants
Spent solvents recovery
Spent solvent recovery plants recycle spent solvents that constitute a significant share of hazardous waste. Spent solvents are mostly critical fluids to be processed due to the presence of several contaminants that frequently cause heavy scaling of the unit operations involved.
Overview
Show more Show lessIn our solvent recovery plants, the unit operations involved are:
- Thin film evaporator (TFE)
- Distillation columns
The TFE acts as a reboiler or vaporizer and facilitates handling highly scaling or thermosensitive feeds, whose components (the recovered solvents) are separated using dedicated distillation columns, operating at specific vacuum levels.
Plants can be designed with either or both (together) unit operations.
Features and rangeability
Show more Show lessWe customise the design of solvent recovery plants according to the feed composition and the separation targets. The typical operating capacity is shown below.
- Feed flow rate: 50 L/h to 20 m3/h
- Pressure: 1 mbar(a) to atmospheric pressure
Using a thin film evaporator as the main process unit facilitates handling the extremely viscous fractions normally present in the evaporator liquid discharge, thus achieving maximum solvent recovery.
Heat recovery from the heat exchanger network can be achieved to minimise energy consumption.
Spent solvent recovery plants can be supplied unassembled or preassembled as a modular skid, to minimise installation operations at the customer’s site.
The most suitable material is selected depending on the nature of the spent solvents and the operating conditions.
The main materials usually selected are the following:
- Stainless steel
- Duplex or super duplex stainless steel
A wide range of services from technical feasibility studies to revamping existing plants is also available.
Key benefits
Show more Show less- Volumes and cost reduction for off-site disposal of waste solvents
- Solvent purification and re-use
- Minimising fresh solvent make up
- Implementation of waste hierarchy
- Customised design
- Bespoke thermal configuration
- Minimum footprint requirement
- Maximum energy savings
- Minimum maintenance downtime thanks to optimised cleaning procedure
- High automation level
- Remote assistance and remote supervision
If a customer wants to conduct solvent recovery within a production site and also address the residual wastewater treatment, we are able to design the ideal solution that seamlessly integrates with the customer’s core production processes.
Applications
Show more Show lessRegeneration is applicable to different solvents and mixtures, such as:
- Oxygenated solvents (e.g., methanol, ethanol, propanol, acetone, acetates, glycols, ethers)
- Hydrocarbon solvents (e.g., toluene, xylene, hexane, cyclohexan)
- Halogenated solvents (e.g., dichloromethane, chloroform)
- Nitrogen or sulphur solvents (e.g., acetonitrile, DMSO)
Generated by the following multiple industries:
- Agrochemicals
- Cosmetic
- Fine chemicals
- Paints & Coating
- Pharmaceutical
- Rubber & Plastic
We design both plants dedicated to solvent regeneration for customers whose main business is exhaust solvent collection and recovery as well as plants that selectively treat solvent rich waste streams, to directly recycle the solvent back to the main production process.
This is conducted by:
- Modifying the existing plants to improve capacity and/or performance (brownfield)
- Designing new regeneration plants (greenfield)
Given the great variety of industrial processes and solvent mixtures, we identify the specific solution to address the customer’s needs by conducting tests at the laboratory and pilot plant scale, as well feasibility studies at our R&D centre.
References
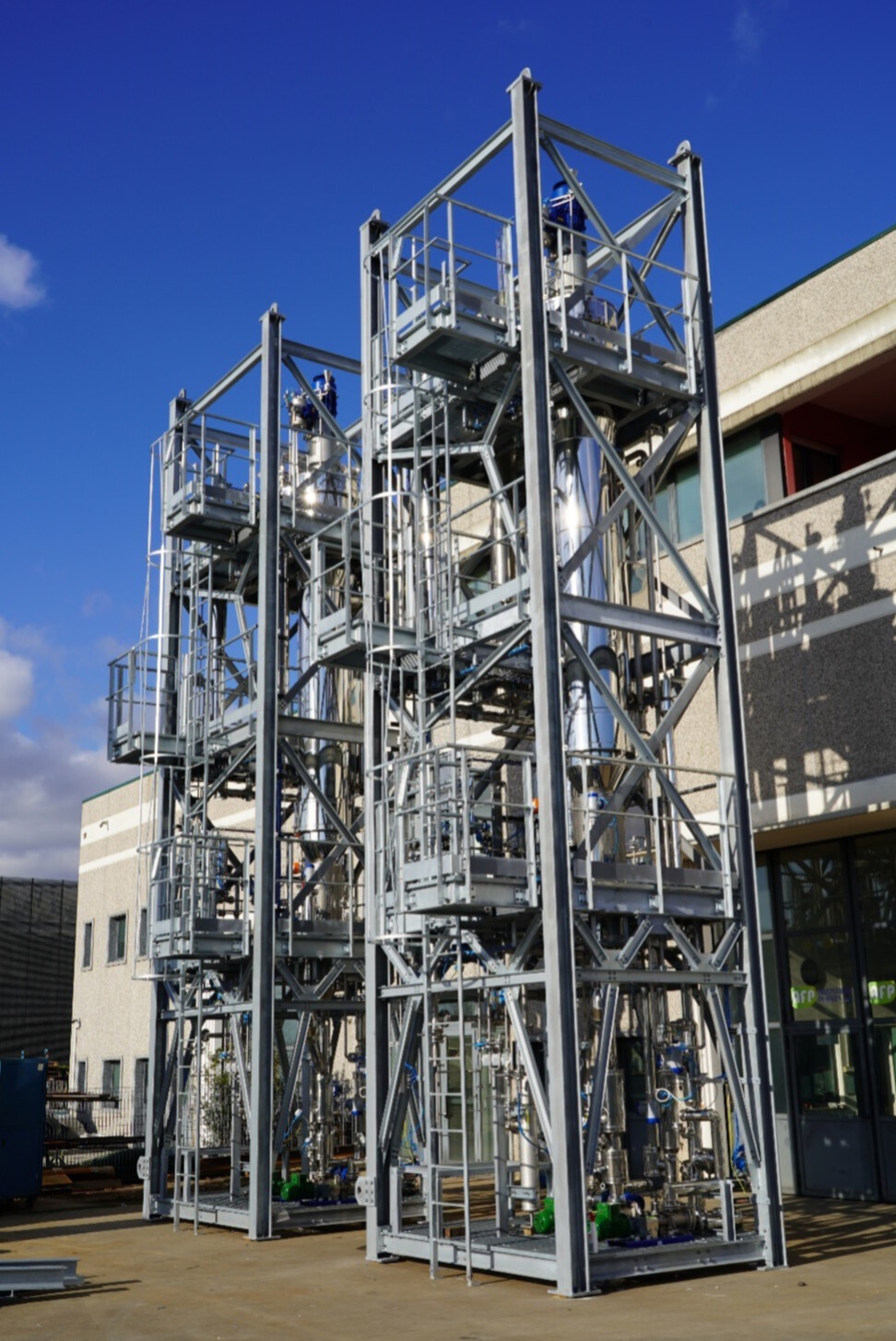
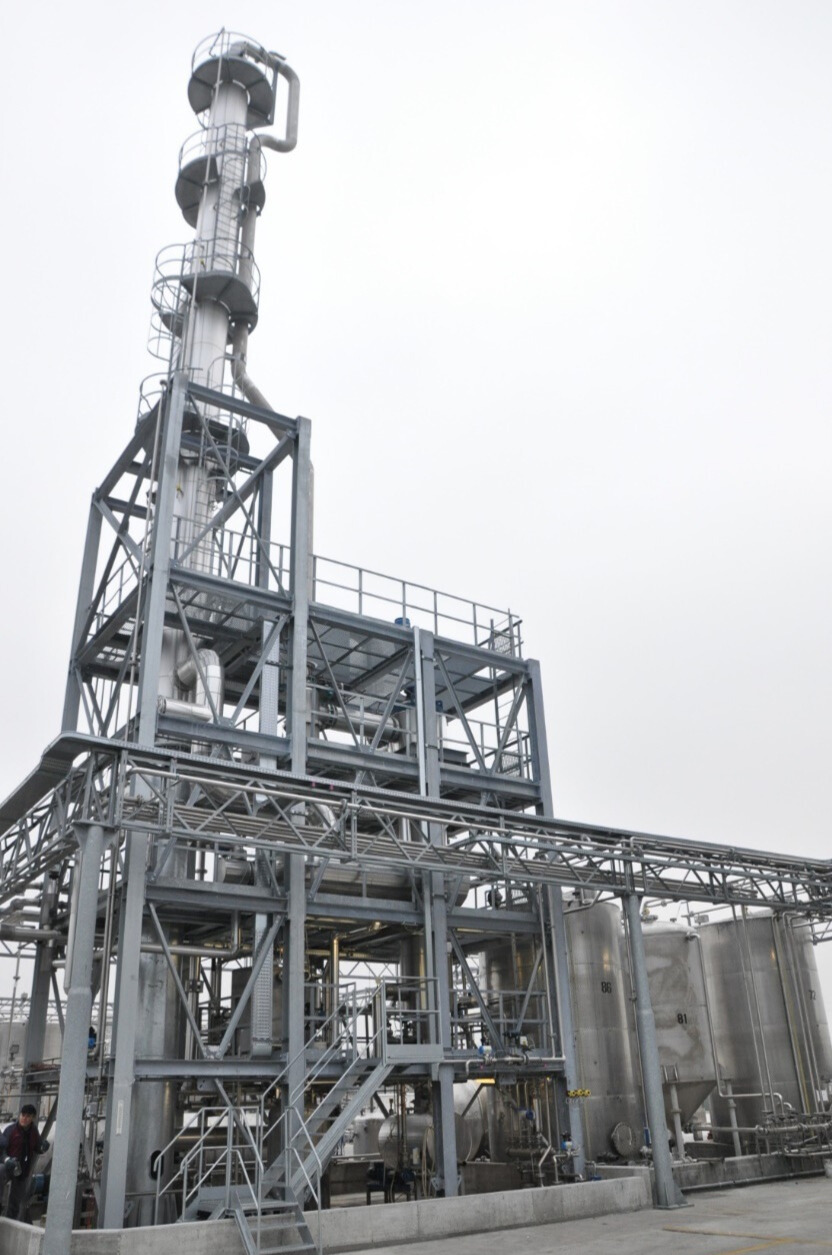
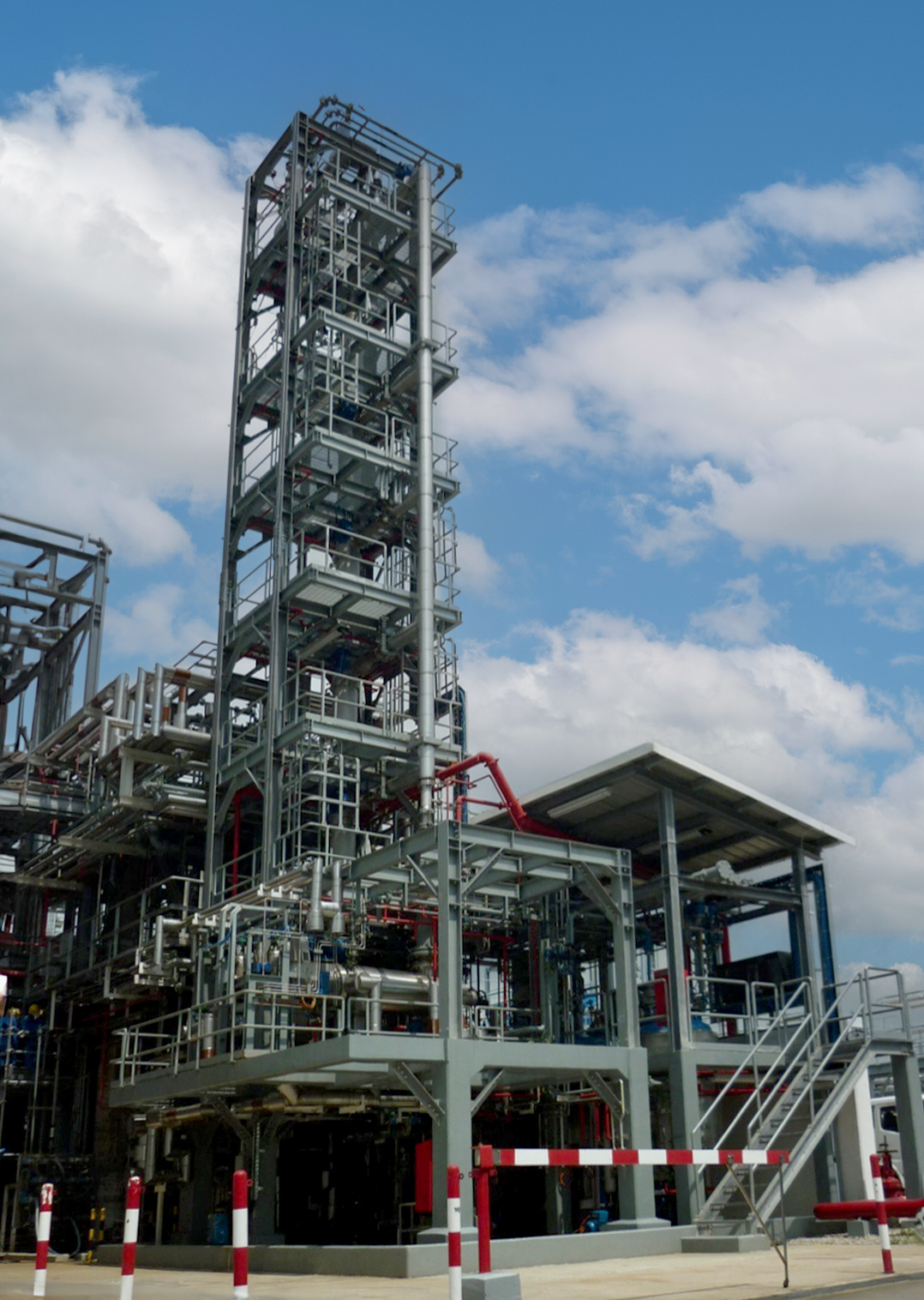
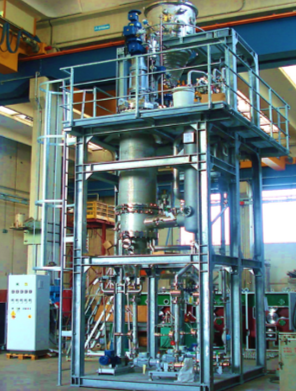