Plants
Wet oxidation – TOP technology
Wet oxidation (WO) treats wastewater having high COD content and/or containing refractory compounds that are hard to degrade.
WO consists in the oxidation of dissolved and suspended pollutants at elevated temperature and pressure using oxygen, or air, as an oxidizing agent. The elevated operating pressure maintains water in the liquid phase and improves the oxidation rate by increasing dissolved oxygen concentration: pollutants are effectively converted to carbon dioxide, water, and intermediate oxidation products.
The WO effluent stream is detoxified, odour and colour are almost removed and its COD content is strongly decreased. The remaining COD is mostly represented by highly biodegradable, low molecular weight compounds that can be treated in standard sections of a wastewater treatment plant (WWTP).
Operational conditions are selected in view of the nature of the waste and required abatement performances and can be divided into three main ranges:
- High pressure systems
- Medium pressure systems
- Low pressure systems
Catalytic wet oxidation can also be employed to achieve greater destruction operating at a lower temperature and pressure or reduced oxidation time: the aqueous stream is mixed with a catalyst before undergoing the oxidation process.
Overview
Show more Show lessA WO plant mainly consists of the following sections.
- From the storage tank, the feed is sent to the WO package with pumps, increasing the stream pressure up to the reactor operating pressure.
- The wastewater is then mixed with compressed air or oxygen; compressors are used to increase the air pressure.
- The bi-phase raw mixture is heated with an external heat source and fed into the reactor where a proper residence time to reach the target performances is provided.
- The oxidation process involves exothermic reactions which lead to increased reactor temperature.
- Heat from the reactor is partially recovered with a feed-effluent heat exchanger preheating the raw water feed.
- The reactor effluent, after the feed/effluent heat exchanger, is cooled with cooling water.
- Cold treated wastewater is sent to a flash separator to allow the disengagement of the off-gases from the liquid.
- Process off-gases from the separator are usually routed to further treatments (e.g., thermal oxidizer).
- The liquid effluent undergoes final polishing typically by biological treatment. If required, a pH adjustment can be added to neutralize the stream.
Features and rangeability
Show more Show lessWe customise the size of the WO plant according to the type of waste to be treated and the customer’s performance expectations. Typical operating parameters are reported below.
- Temperature: 120°C to 300°C
- Pressure: 5 barg to 170 barg
- Feed flow rate: 0,2 m3/h – 50 m3/h
The most suitable material is selected depending the nature of the wastewater and the operating conditions.
The main materials usually selected are the following:
- Stainless steel
- High performance alloys
- Titanium
WO plants are supplied as pre-fabricated modules (skid mounted units), the minimising installation operations to be performed at the customer’s site.
Wet oxidation plants are typically coupled with biological treatment for effluent polishing and can be integrated with stripping for high solvent content or relevant nitrogen contamination.
Key benefits
Show more Show less- Near complete detoxification of the wastewater (increased biodegradability)
- Relevant savings on waste disposal costs
- Reduced environmental footprint
- Maximum operating flexibility (in feed composition and flowrate)
- Minimum maintenance downtime due to cleaning procedure
- Maximum energy savings
- High automation level
- Reliability
Applications
Show more Show lessA wide range of applications are possible for both municipal and industrial wastewater, having high COD content and/or containing refractory contaminants, including hard to degrade spent caustic water.
Municipal and industrial wastewater
Typical feed for wet oxidation comes from a broad range of industries:
- Chemical (synthesis processes)
- Iron and steel industry
- Landfill
- Petrochemical
- Pharmaceutical
- Pulp and paper
- Textile dyeing
Efficacy has been checked on hundreds of contaminants from antibiotics to pesticides, phenols, surfactant agents, landfill leachates obtaining:
- Up to 80% COD
- Up to 99% removal of volatile dissolved and suspended solids
Spent caustic water
Typically, the WO process is applied to treat spent caustic water from ethylene plants or refineries having high COD content (from 10,000 to 200,000 mg/l) and different contaminants such as sulphides, mercaptans, thiosulphate, phenolic and naphthenic compounds.
Depending on the contaminant’s nature and the target reduction sought, different operation conditions are applied.
The broad range of industrial processes generates extensive wastewater compositions and, whether easy or difficult to treat, each type of wastewater requires a customised process and a bespoke plant design.
We provide support to our customers conducting tests at the laboratory and pilot plant scale, as well feasibility studies leveraging our R&D centre and multi-disciplinary teams.
References
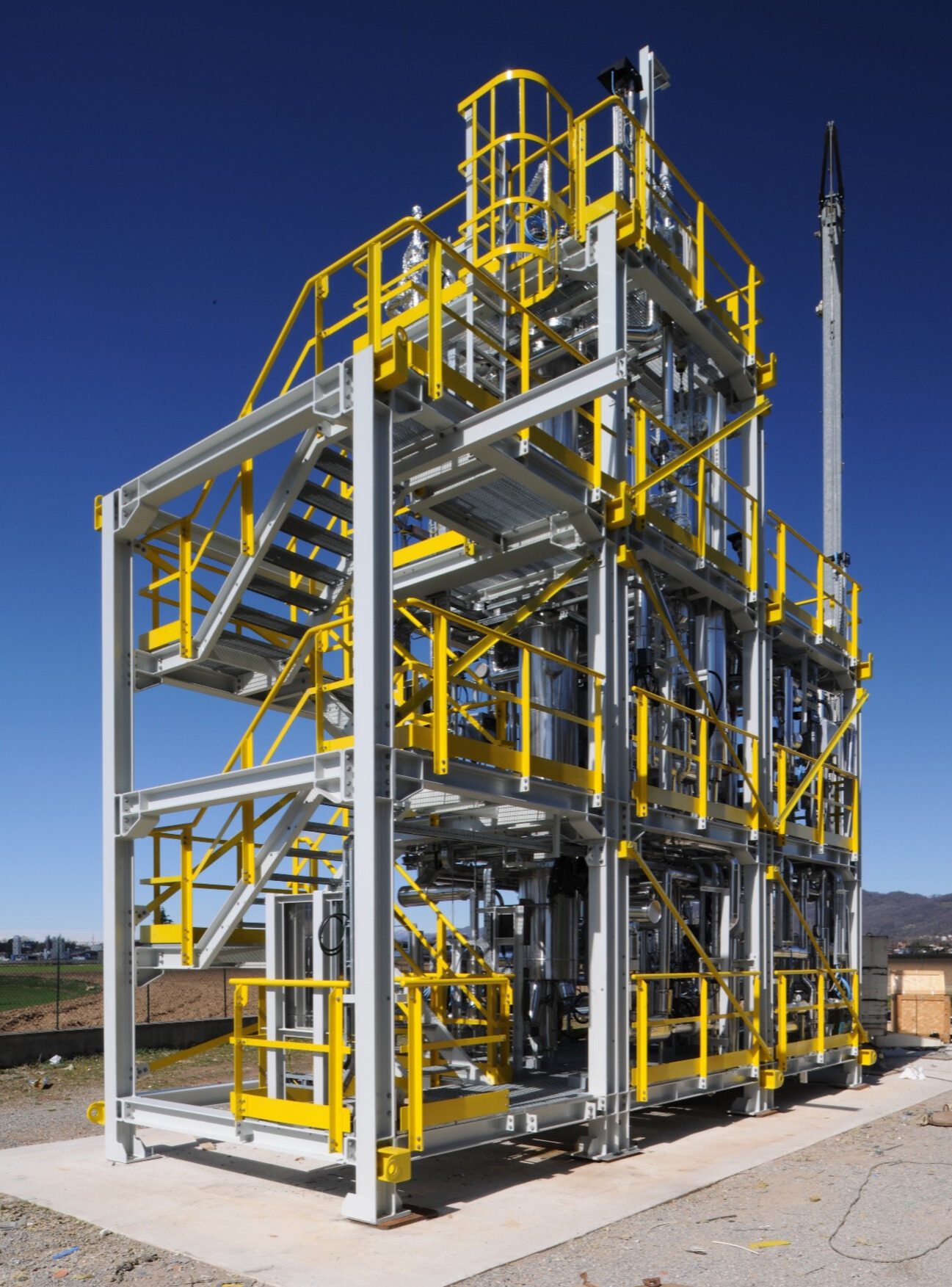

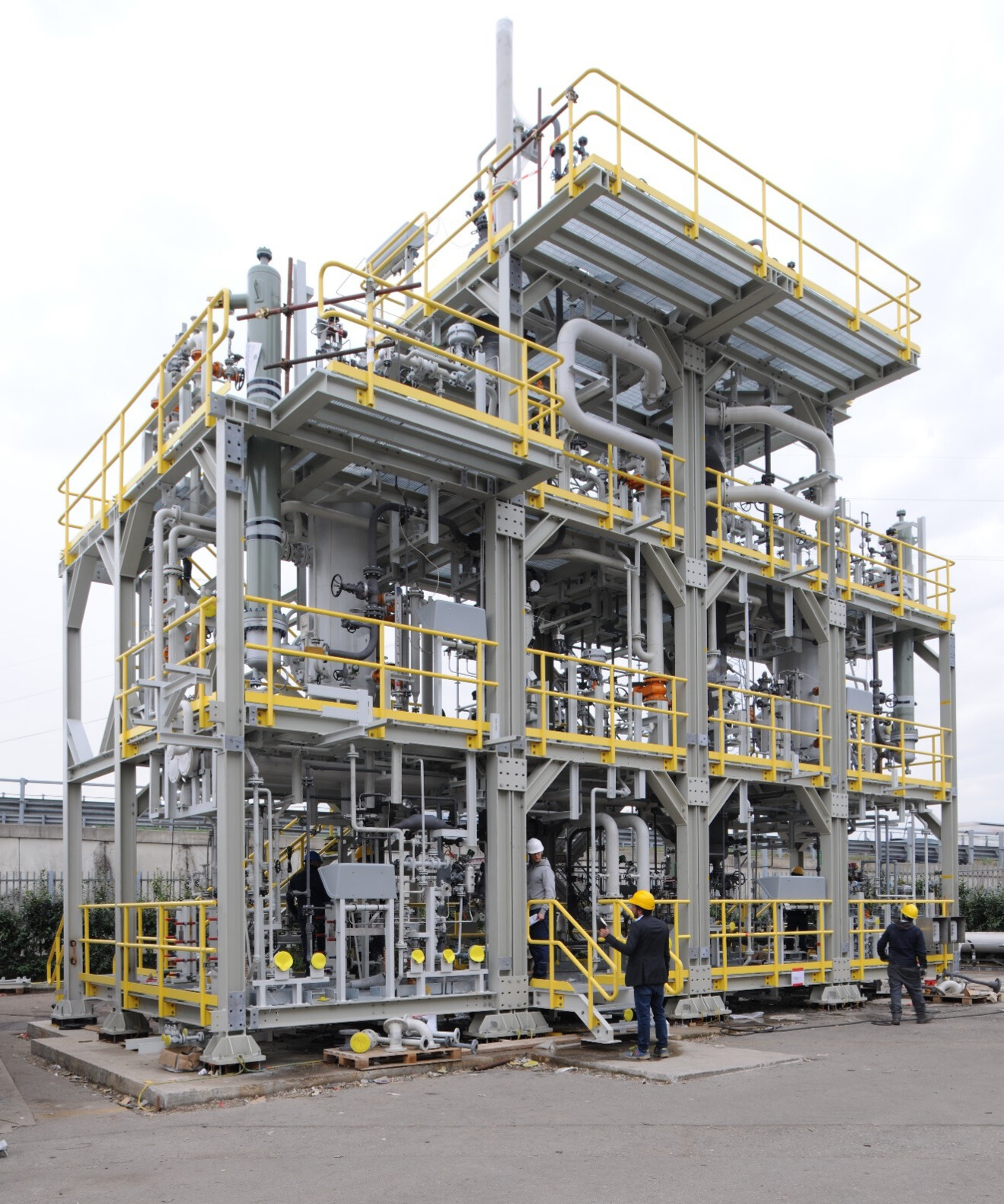
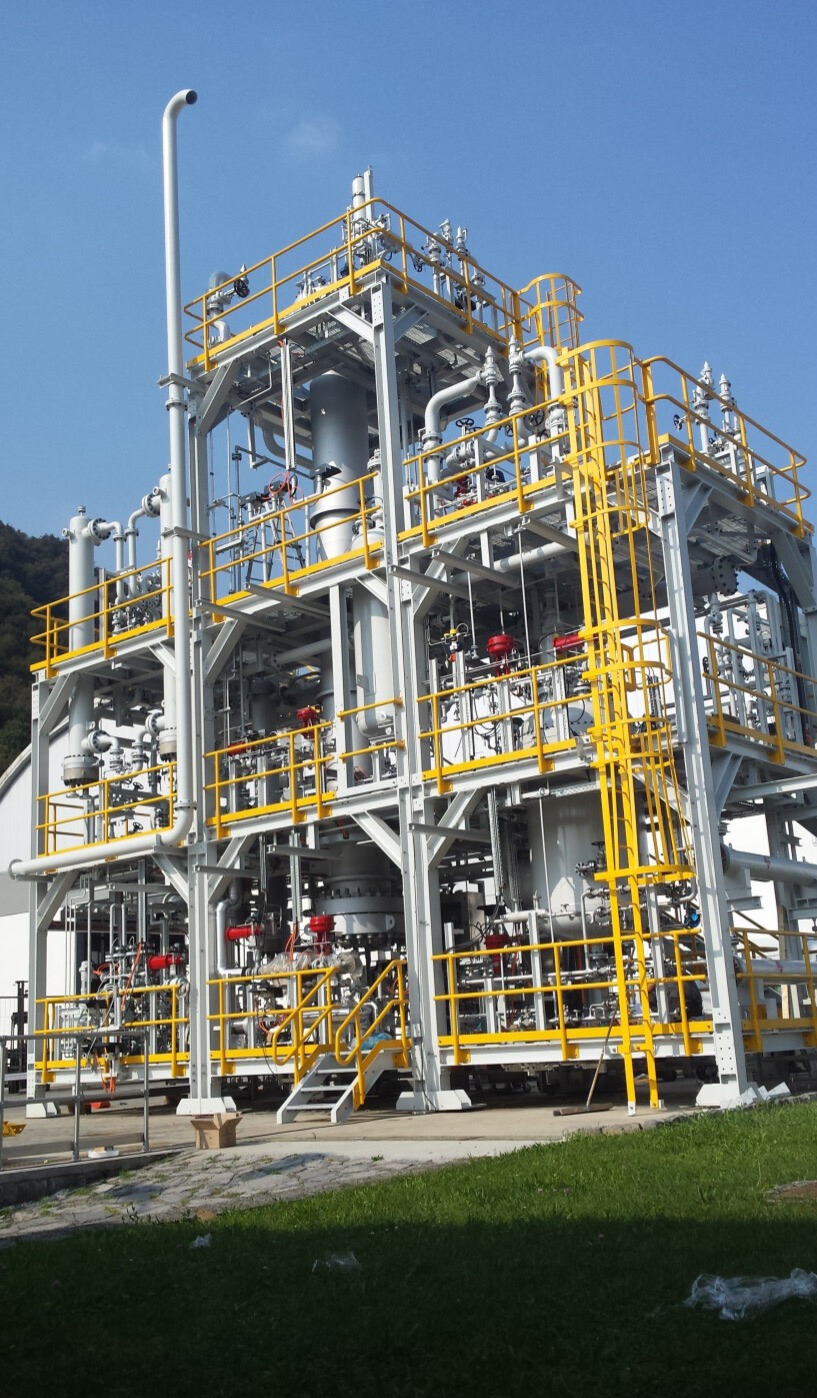
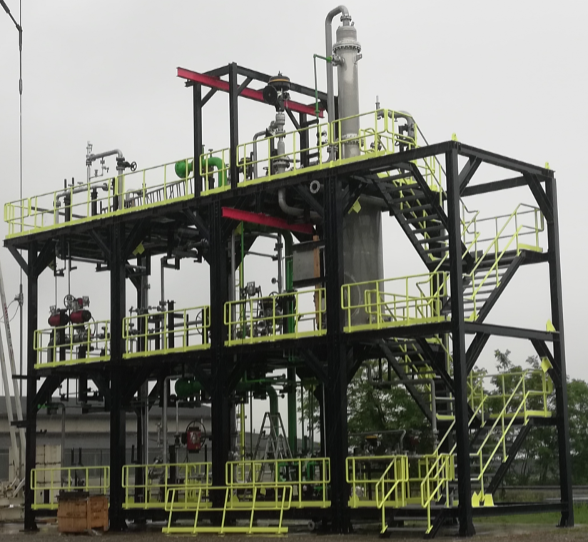
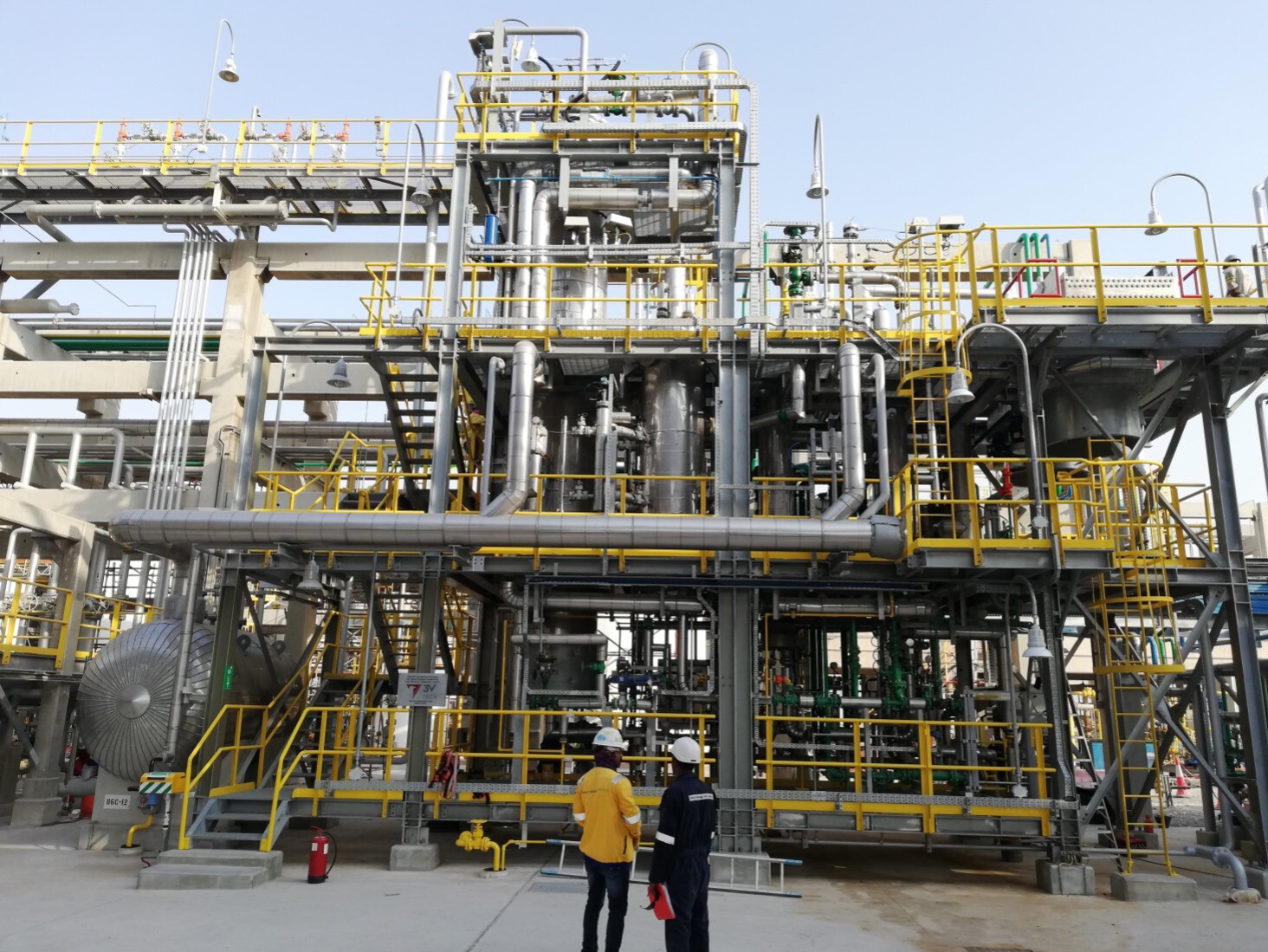
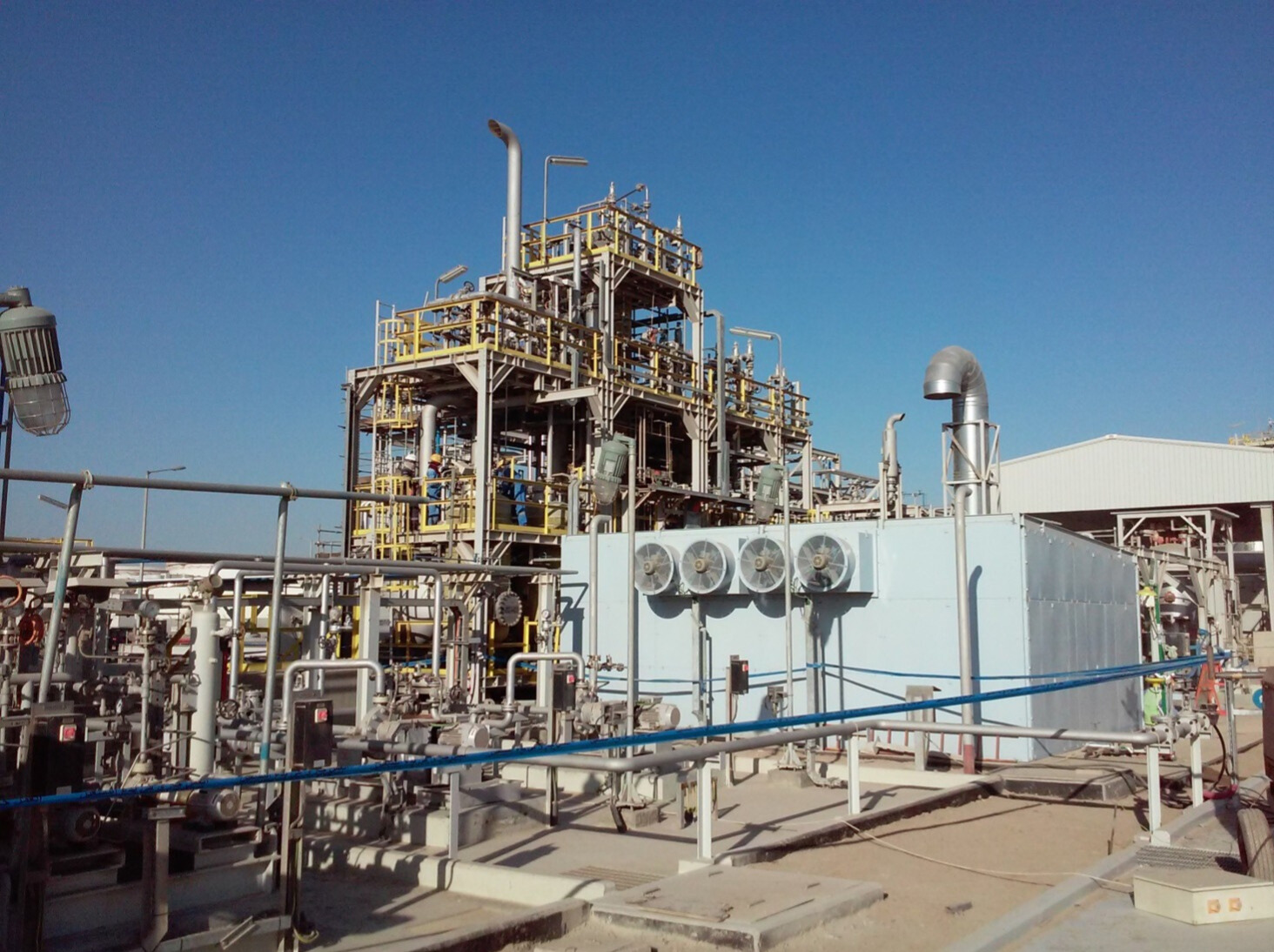
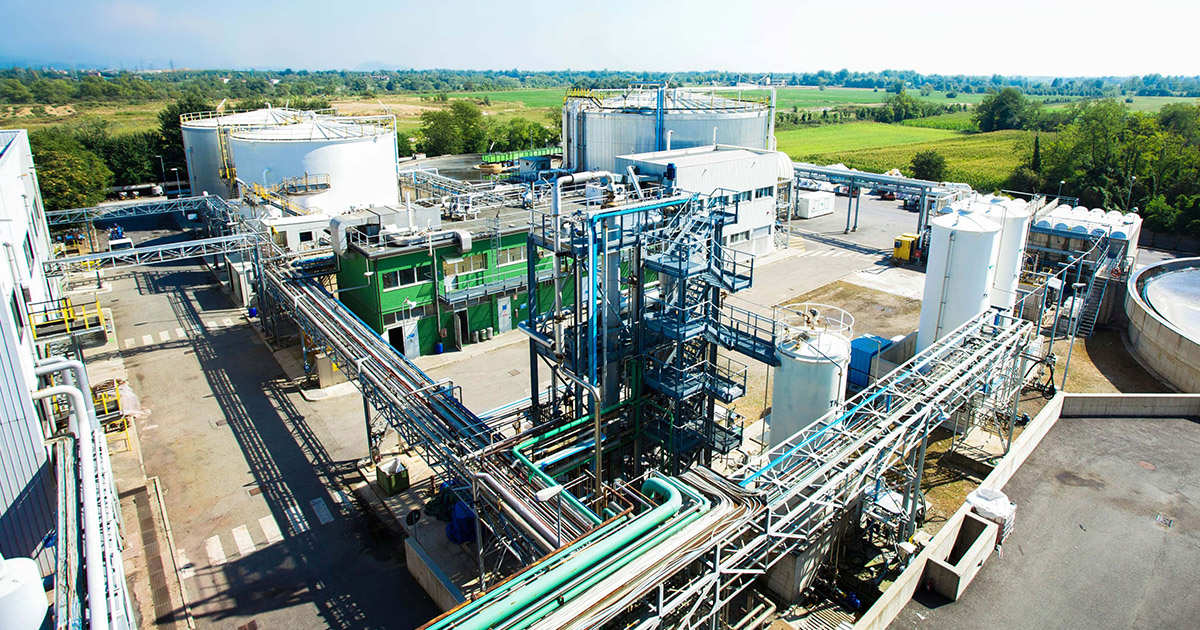