Plants
Polymers concentration & devolatilization
The purification stage in polymer production is a key step to achieve the final product’s desired properties and performances. Solvents, residual monomers and oligomers need to be removed before the last processing steps.
All these volatile impurities can be eliminated by evaporation in a single stage or in multiple stages depending on the polymer characteristics, the initial volatile impurity content and the target sought.
When the initial content of polymer is low (or the solvent content is high), a concentration step is conducted before devolatilization.
Overview
Show more Show lessOur polymer purification plants usually include the following steps and unit operations:
- Concentration in the case of low polymer content.
This is generally obtained using flash or falling film evaporators, suitable for low to medium viscous fluids, or forced circulation evaporators for medium to high viscous fluids. - Devolatilization using wiped film evaporators (WFE) or thin film evaporators (TFE) and short path evaporators (SPE) are excellent to handle viscous and temperature sensitive products such as polymers.
The devolatilization step is generally run under vacuum and may be conducted in several stages operating at different temperatures, pressures and feed rate conditions. When the purity sought is very high or if high boiling impurities are present, usually a final stage, using a short path evaporator, is required to operate at very high vacuum to avoid any product degradation.
Energy consumption may be optimised by:
- Using hot water from cogeneration
- Using waste energy (e.g., exhaust gas, steam condensate, process condensate)
- Combining the abovementioned technologies
Features and rangeability
Show more Show lessPolymer purification plants are customised according to the customer’s needs and expectations; typical features are reported below.
For products having high viscosity, a wiped film evaporator or a thin film evaporator can also be used.
Devolatilizazion step
- Various rotor blade designs for WFEs or TFEs are possible, including special blades for polymers.
- Available also as skid mounted units to minimise installation operations at the customer’s site.
The most suitable material is selected based on the nature of the product and operating conditions.
The main materials usually selected are the following:
- Stainless steels
- Super duplex stainless steels
- Nickel alloys (e.g., Hastelloy® HC22, Inconel® 600)
A wide range of services from technical feasibility studies to revamping existing plants is also feasible.
Key benefits
Show more Show less- Customised design
- Optimised energy consumption
- High automation level
- Remote assistance
- Easy cleanability
Specific benefits – wiped film evaporators or thin film evaporators
- Optimised heat transfer surface, thanks to the high heat transfer coefficient and the possibility to operate with a wide difference in temperature (∆T).
- High evaporation rate and short residence time with strong reduction of product degradation issues.
- No fouling problems thanks to the low residence time, high turbulence and continuous cleaning of the heated surface.
Specific benefits – Short path evaporators
- No product degradation thanks to very low operating pressure, low evaporation temperature and short residence time.
- High product purity thanks to the possibility to devolatilize also very high boiling impurities.
Applications
Show more Show lessEvaporation plants can purify different kinds of polymers and specialty polymers, such as, for example:
- Acrylic resins
- Acrylonitrile butadiene styrene (ABS)
- Epoxy resins
- Phenolic resins
- Polyacrylonitrile
- Polyester
- Polyethylene
- Polybutadiene
- Polycarbonate
- Polypropylene
- Polystyrene
- Polyurethane
- Polyvinyl alcohol (PVA)
- Silicone oils
- Styrene acrylonitrile resin (SAN)
The wide range of polymers and impurities results in extensive product compositions. To identify the specific process solution, we perform process simulations and testing, leveraging our multidisciplinary teams and R&D centre capabilities.
References
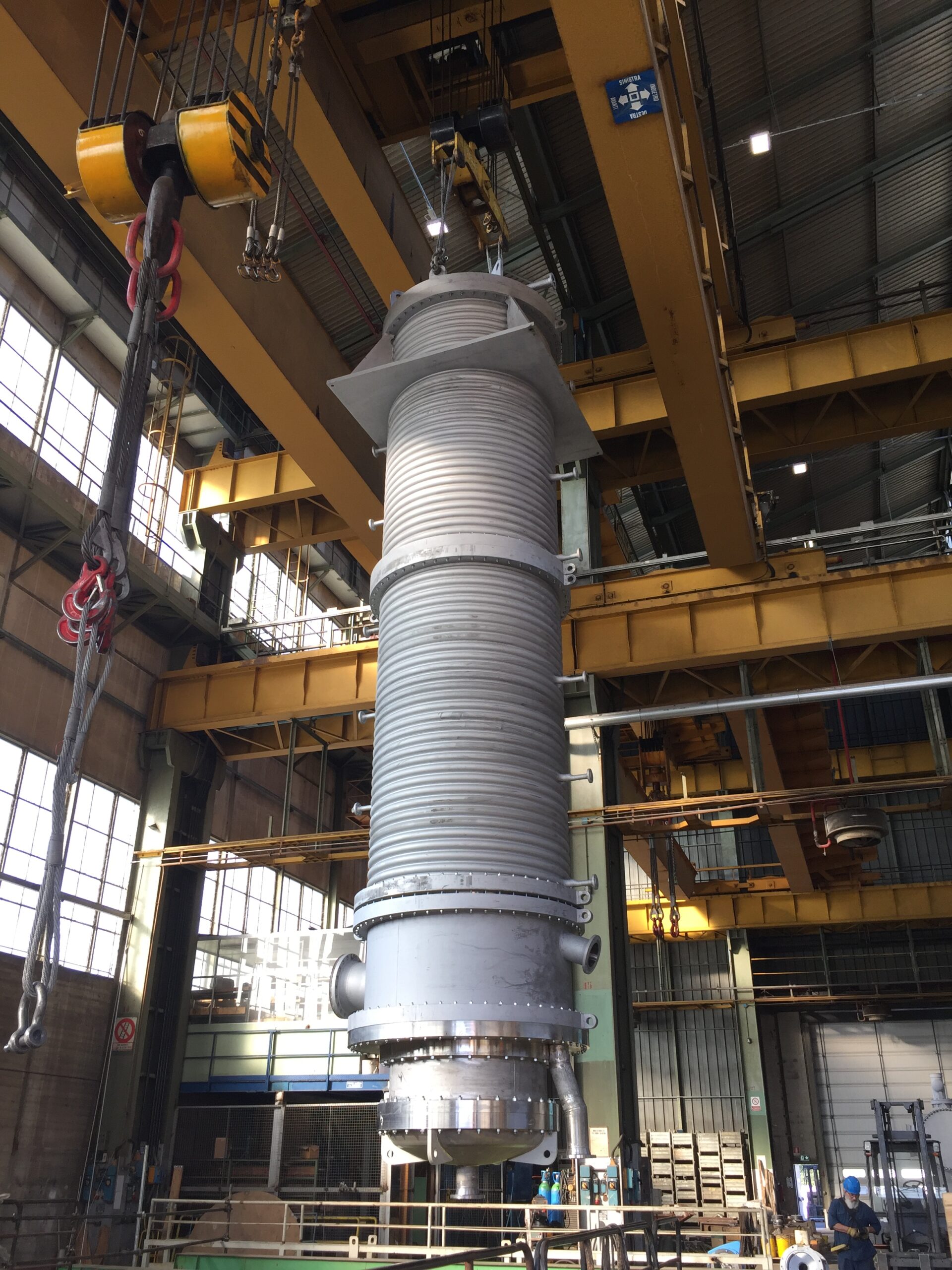
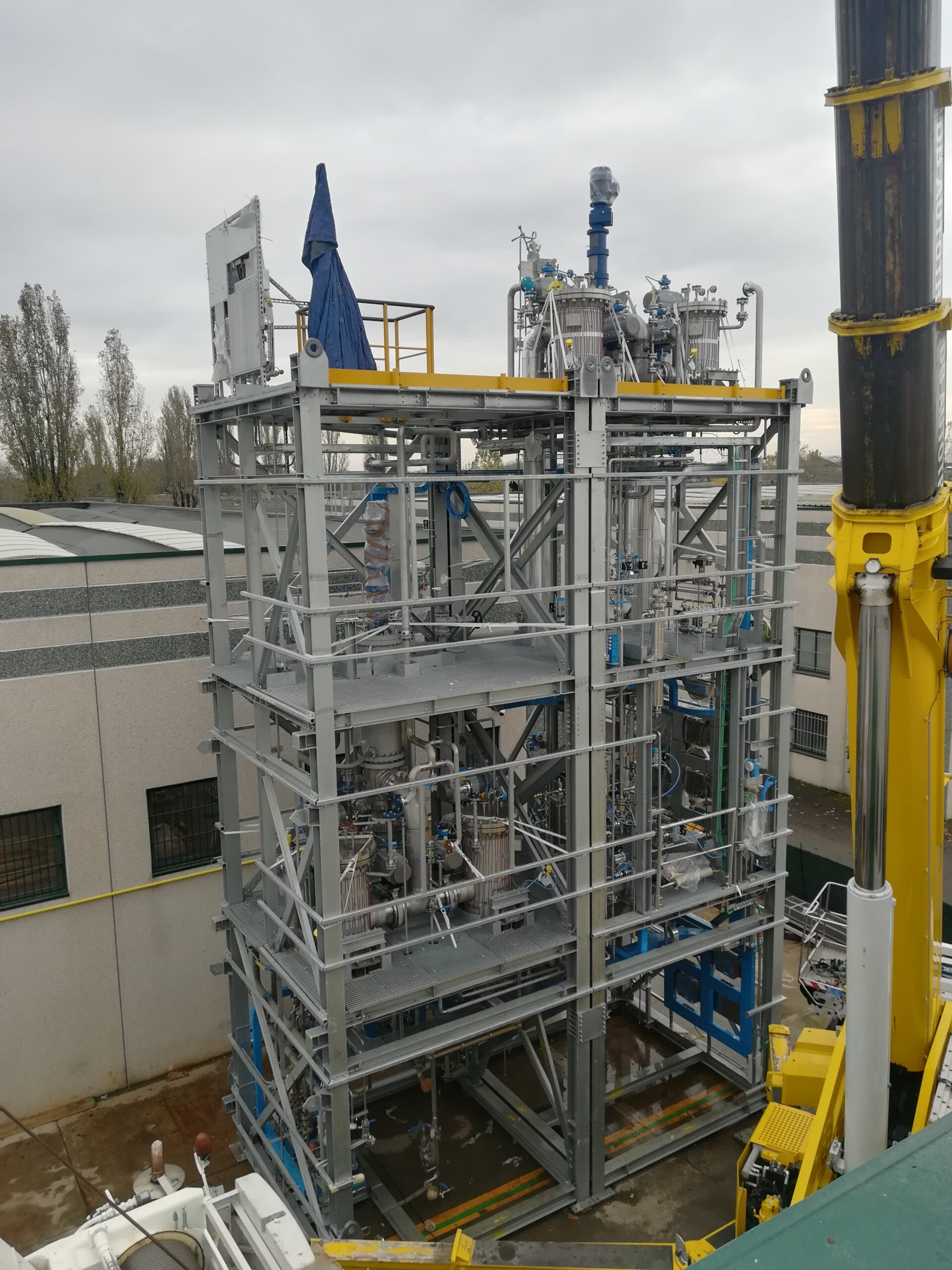
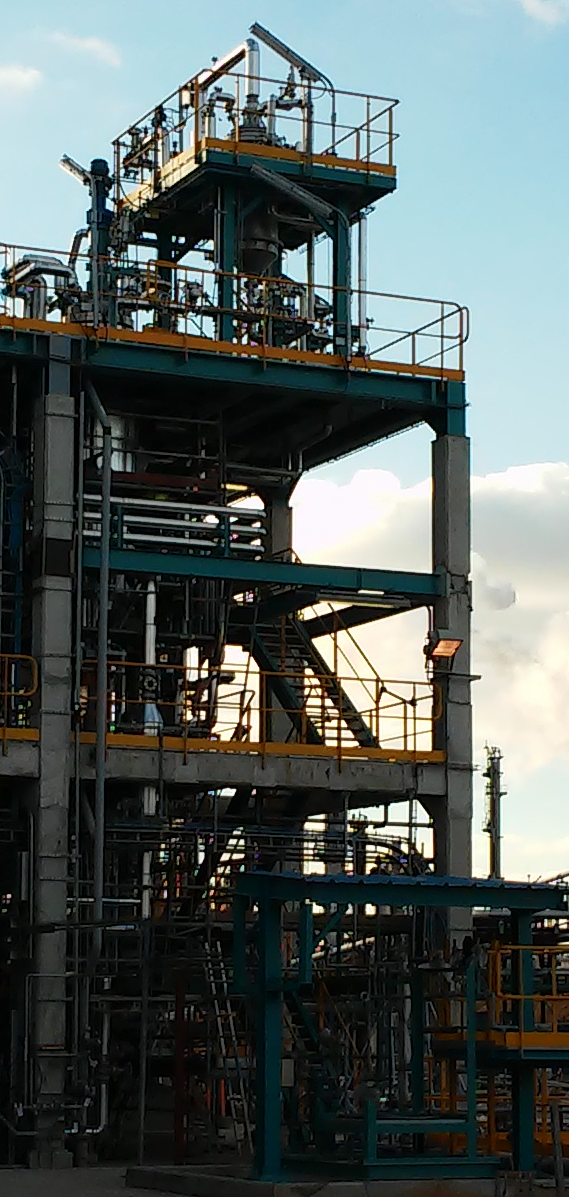
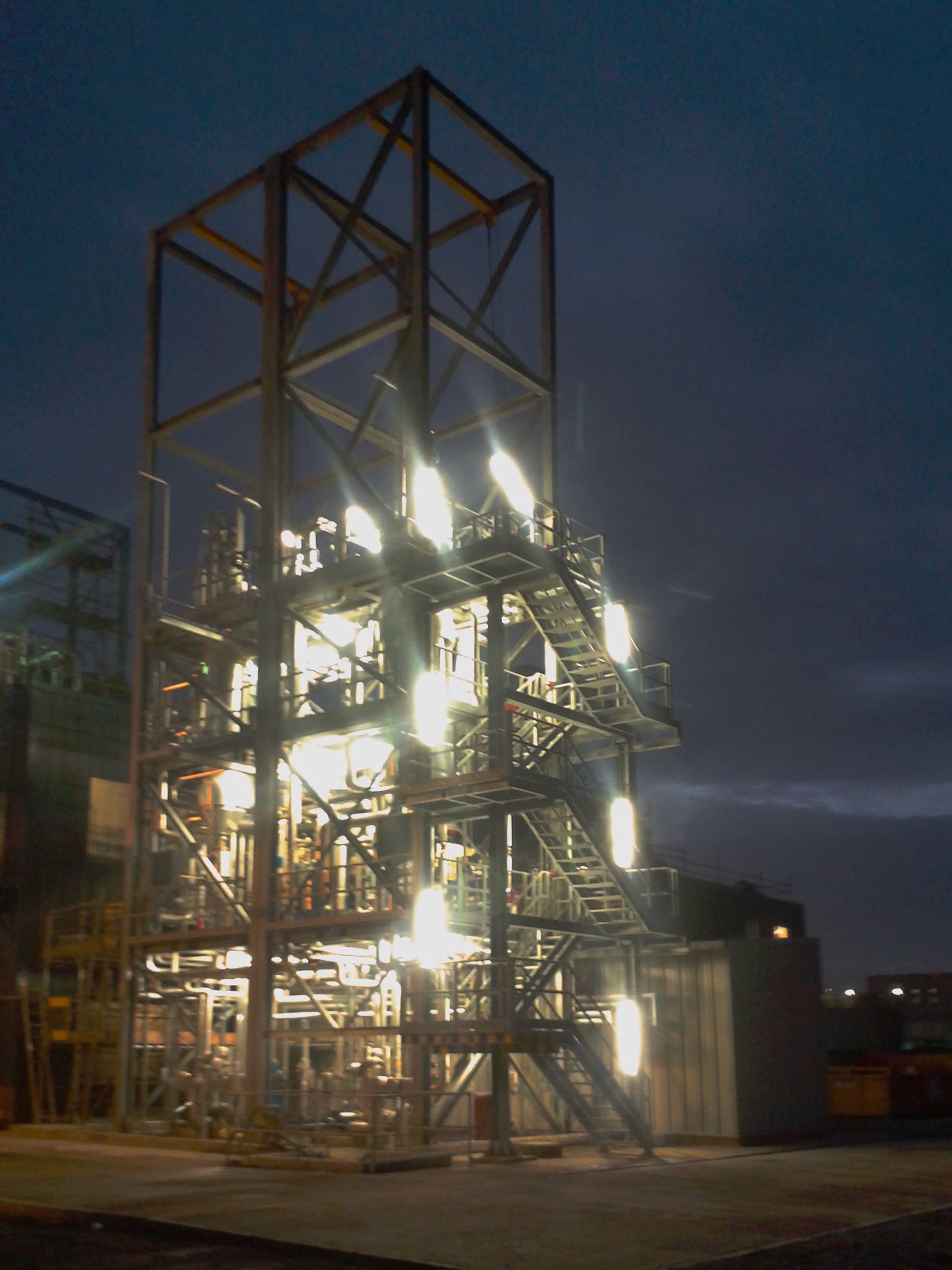
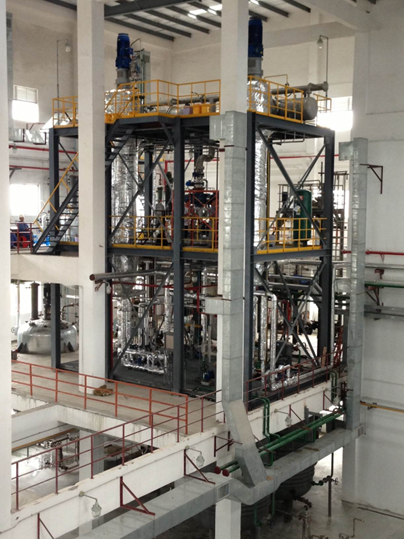