Plants
Deep neutralization
The deep neutralization process allows toxic and harmful compounds to be removed from alkaline liquid waste streams.
The process consists in the acidification of wastewater to release and then remove the acidic components and, consequently, the relevant COD.
The deep neutralization process is the proven technology to treat oil refinery and petrochemical spent caustic water characterised by a high concentration of toxic compounds such as sulphides, mercaptans and naphthenic acids.
Overview
Show more Show lessA typical plant consists of the following four sections.
- Acidification section: pH of the spent caustic wastewater is lowered by adding concentrated acids, such as sulphuric acid (98%wt), to release the acidic components that were captured in the alkaline caustic solution.
- Separation section: light & oily compounds released during the acidification process are separated from the wastewater stream by skimming.
- Stripping section: off-gasses released due to pH reduction (typically hydrogen sulphide and mercaptans) are removed by stripping (fuel gas or nitrogen are usually used as stripping media).
- Neutralization section: the pH of the treated wastewater is adjusted to neutral pH.
The plant is operated at low pressures and temperatures.
Features and rangeability
Show more Show lessWe customise the size of the deep neutralization units based on the type of wastewater to be treated and the customer’s needs. Typical operating capacity and treatment efficacy are listed below:
- Feed flow rate: 0,5 m3/h- 20 m3/h
- COD reduction: more than 90%
Available as skid mounted units to minimise installation operations at the customer’s site.
Key benefits
Show more Show less- High wastewater detoxification
- Reduced environmental footprint
- Operating flexibility
- Minimum maintenance downtime due to cleaning procedure
- Maximum energy savings
- High automation level
Applications
Show more Show lessDeep neutralization is a treatment option for sulphidic and naphthenic spent caustic water to reduce sulphides and mercaptan content.
For a stronger reduction, including harder to degrade contaminants, wet oxidation plants are the alternative solution.
References
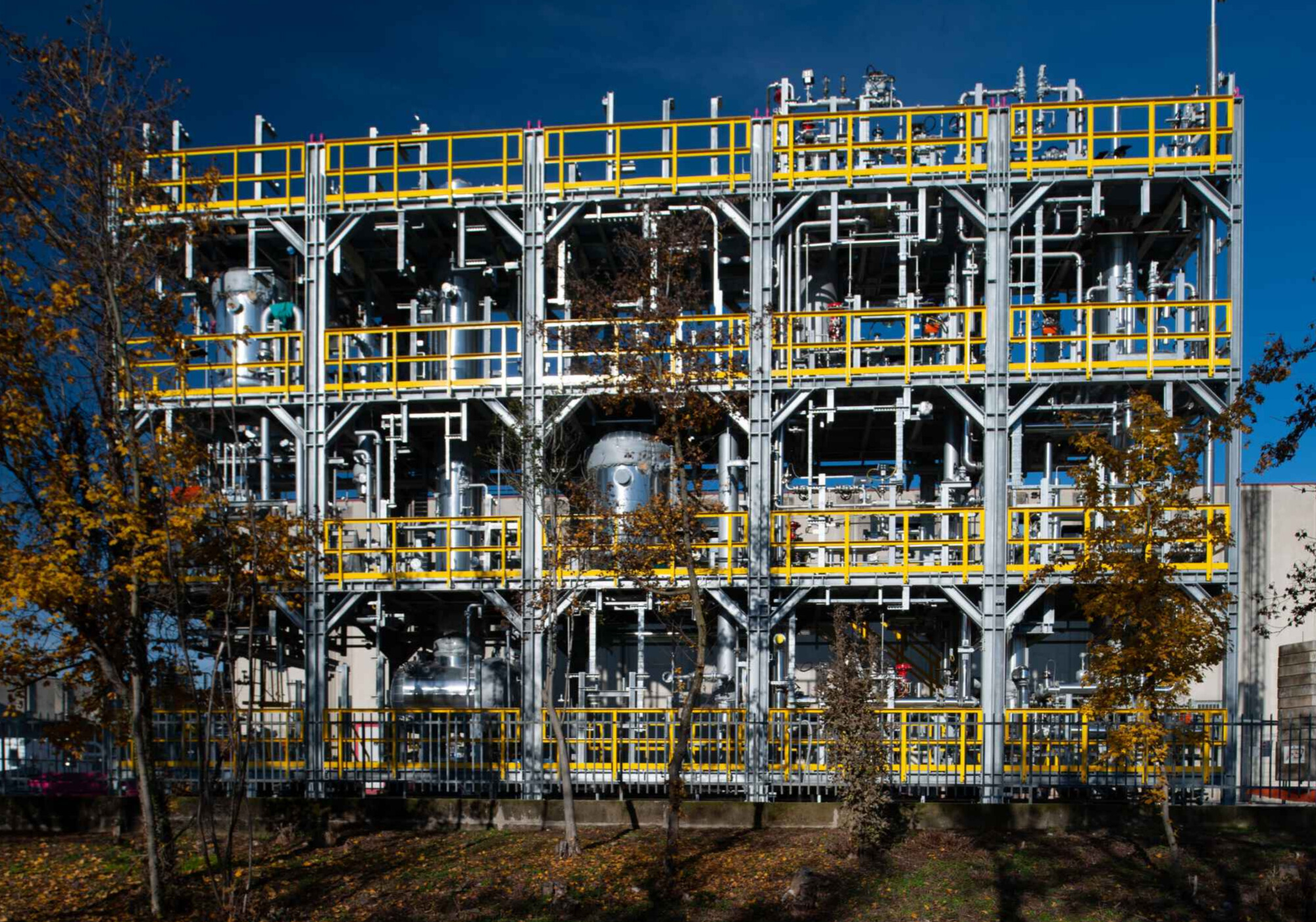