Plants
Glycerine recovery
Glycerine can be produced with different processes and among them it’s of relevant importance the recovery as a by-product of oleochemical industrial processes (production of soap, fatty acids and biodiesel).
Recovery requires multiple treatments, and the concentration and purification steps are critically relevant to achieve the desired final grade of glycerine.
The concentration step, generally required in the case of recovery from spent lye (soap production) or sweetwater (fatty acids production), is intended to reduce the water content before final purification: thermal separation technologies such as evaporation and distillation are commonly applied.
Overview
Show more Show lessOur plants usually include the following steps and unit operations:
- Concentration in case of low glycerine content (spent lye and sweetwater).
After a preliminary purification step with additives and physical separation equipment, the diluted glycerol is concentrated into crude glycerol using falling film evaporators or forced circulation evaporators, usually arranged in a multiple effect configuration for energy consumption optimisation. - Final purification using a wiped or thin film evaporator coupled with a distillation column, operating under vacuum.
During the purification step, impurities like salts, sand and MONG (Matter Organic Non-Glycerol) are concentrated at the bottom of the evaporator, while most of the glycerine is vaporized and fed into a distillation column for final purification.
The bottom fraction obtained from the thin film evaporator, depending on the MONG-to-salt ratio and the acceptable residual content of glycerine, may be a solid or a slurry and, as consequence, two distinct discharge systems are possible:
- For of a solid, the discharge system is composed of a series of collection vessels, pneumatic vibrators and pneumatic valves to enable solid discharge under vacuum.
- For a slurry, a scraping device is incorporated into the evaporator cone and the product is recovered with a pump.
Features and rangeability
Show more Show lessConcentration and purification plants are customised according to the customer’s needs and expectations; typical features are reported below.
Available also as skid mounted units to minimise installation operations at the customer’s site.
The most suitable material is selected depending on the feed composition and operating conditions.
The main materials usually selected are the following:
- Stainless steels
- Super duplex stainless steels
- Nickel alloys (e.g., Hastelloy® HC22, Inconel® 600)
A wide range of services from technical feasibility studies to revamping existing plants is also feasible.
Key benefits
Show more Show less- Wide range of applications, from low to very high (solid) discharge concentrations
- Customised design
- Combination with other process units
- Bespoke thermal configurations
- Optimised energy savings
- High automation level
- Remote assistance
- Easy to clean
Specific benefits – wiped film evaporators or thin film evaporators
- Optimised heat transfer surface, thanks to the high heat transfer coefficient and the possibility to operate with wide differences in temperature (∆T)
- High evaporation rate and short residence time with strong reduction of product degradation issues
- No fouling problems thanks to the low residence time, high turbulence and continuous cleaning of the heated surface
Applications
Show more Show lessThe recovery of glycerine as a by-product of oleochemical industrial processes (production of soap, fatty acids and biodiesel).
More about our oleochemicals purification plants
Depending on the specific properties of the product (concentration and impurities content) and the final grade to be achieved, the process needs to be carefully identified through simulation and testing, all of which are conducted at our R&D centre leveraging our multidisciplinary teams.
References
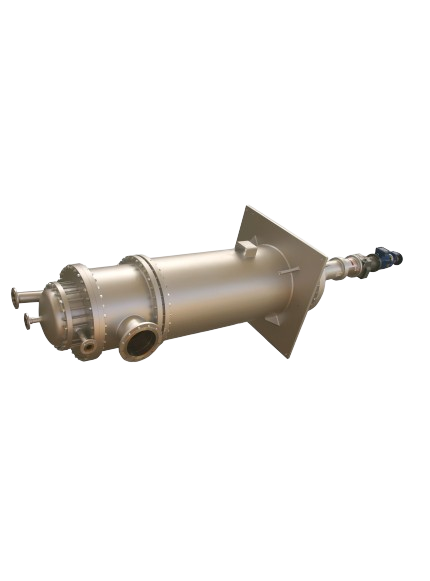
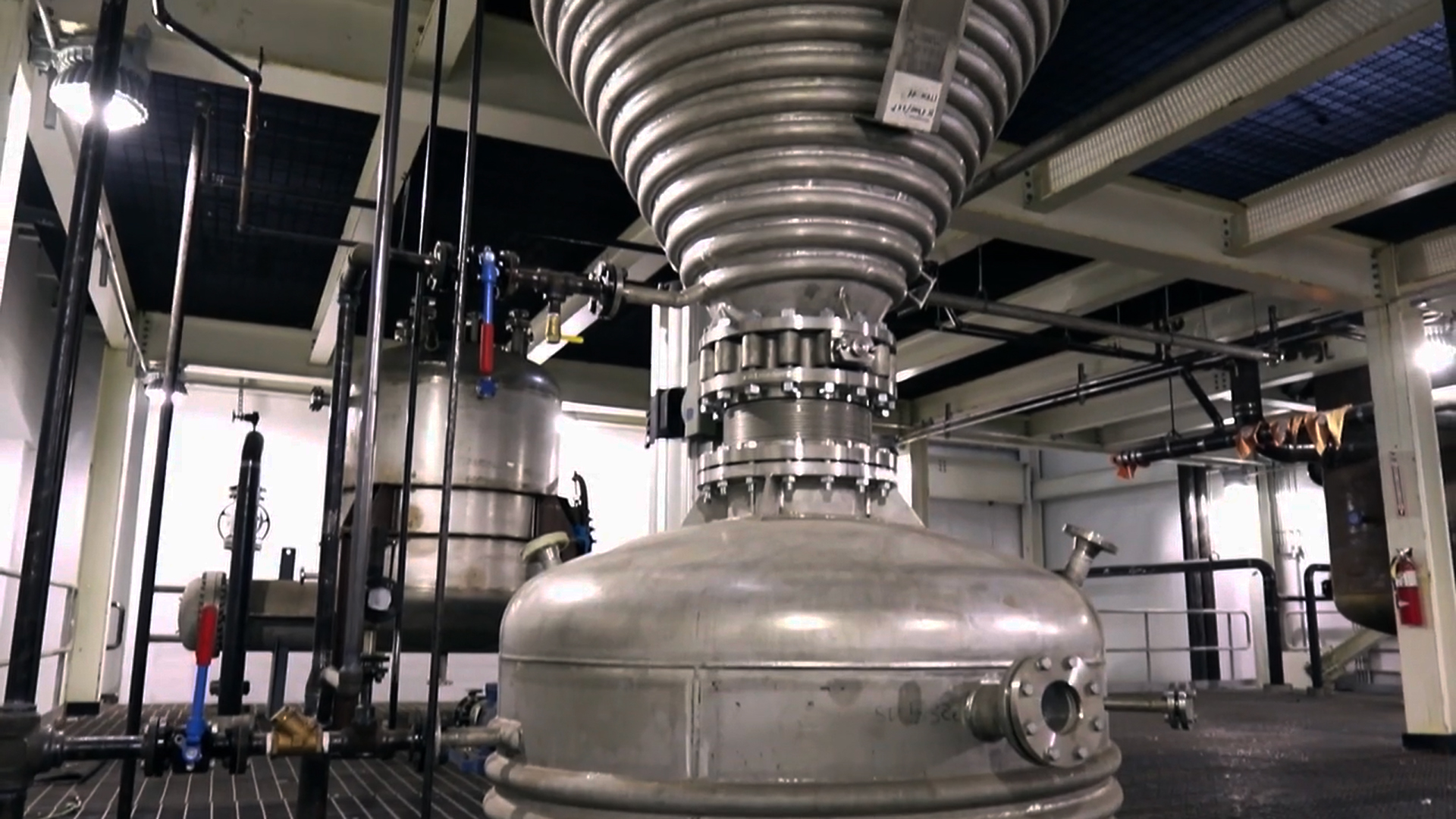